

How many customers not on current pricing? How much revenue have we missed due to not being on current price? How many customer back charges (credits) have we incurred? What is the cost of those back charges? Do we have back charge reasons in a database? What impact does poor execution of the contract have on Account Receivables? Process FMEA OBSERVATION: Controls not in place for many processesġ6 Plan for Data Collection (Measure Phase) Internal Approvalġ5 Controls not in place for many processes
#Six sigma green belt project report examples update#
Solution Accepted Ticket Customer Validate Customer Support Customer Services Satisfaction Approved Create Service Delivery Work Order or Monet Coordinators Approved Ticket Request Create Queue Buy Billable No Coordination Ticket yes yes Request? Update Ticket Resolve Assign Receive Request/ Technician Ticket Equipment Verify Solution Route Buy MMO Ticket for Create P.O. Y2 = Percent of 48-hour orders processed by end of business second dayĭetailed Process Map Process Decomposition Using Swim Lane Business Modellingġ4 Detailed Process Map WARP Implementation Close Problem Y1 = Percent of 24-hour orders processed by end of business next day.
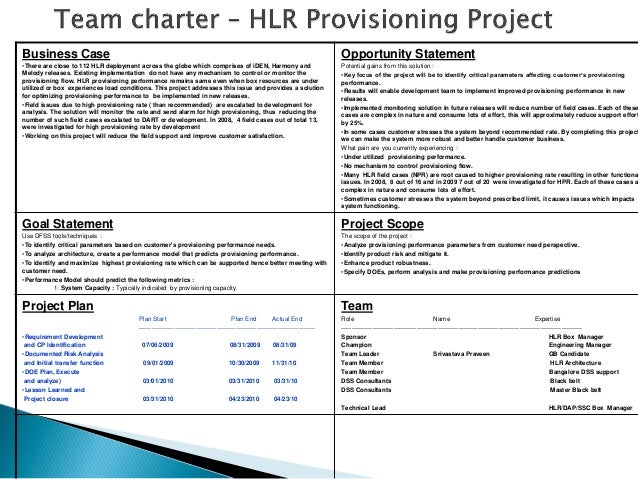
Project Champion or Sponsor: Project Team Leader or Black Belt: Project Team Members: Ad Hoc Members or SMEs:ġ1 Define Measure Analyze Improve Control Improved service performance through less time loss in tickets including wait time.ħ Total ECO Cost $2,226,006 Business Case - COPQ calculationĬost: $2,088 / ECO Total ECO Cost $2,226,006 Reduced wastage in billing disputes 15 mins each) or $20k per annum Soft Benefits: Improve customer satisfaction from less wrong contacts. Wastage of labor in the customer satisfaction survey of 3 mins per defect or $24k per annum. Wasted labor time spent in AMP on finding correct contact data for problem resolution estimated to be 5 min/defect on approx 1656 defects per month or $100k per annum. Operational and Strategic Impact: Hard Benefits: $145k or 1.82 FTE can be delivered in AMP from improved customer contact data. Relevant Metrics: (Usually these are associated with quality- effectiveness, efficiency, time or cost.) Some common metrics are: Response Time (minutes, hours, days …)Ĝycle Time (minutes, hours, days …) Downtime (minutes, hours, days …) Correctness (of information or data) or Error Rate (%) Billability (%) Efficiency (%) Document Error Rate (%)ĝefect rate (%) Availability (of systems) (%, Mean Time Between Failure, Mean Time to Repair) Cost of Poor Quality ($) Rework ($) Repair ($) Warranty ($)Ğxpedite ($) Improvement Targets: 50% reduction in cycle time Increase System Availability from 88% to 98% Operational/Strategic Impact: $60,000,000 improvement to bottom line (this would seem to be a large undertaking) Waiver: A legal document releasing our ownership of the products and services sold.
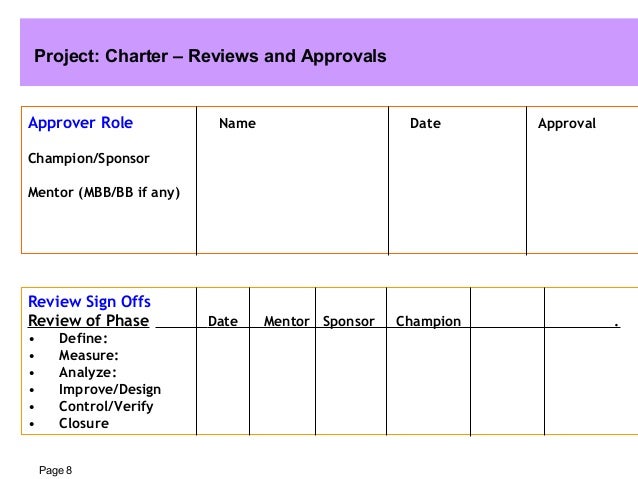
Retainage: Monies that are owed to us and retained by the customer to ensure specific performance of the contract and warranty claims are completed. (Ending AR for Period * Days in Period) / Sales for Period Progress Bill: A temporary billing file that “holds” the invoice until all tasks have been completed. Check: Any form of payment from a customer to us. Backorder: Product or service that was ordered by a customer but not delivered due to out of stock situations. Accounts Payable: Monies owed by us to a vendor or supplier for goods and services received. AP: Accounts Payable AR Representative: Employee responsible for tracking monies owed to us by a customer. Benefits will be evaluated 6 and 12 months following implementation.ĪR: Accounts Receivable Accounts Receivable: Monies owed to us by a customer for goods and services provided. Corrective action plan will be prepared by June 200X, implemented by July 200X. Goal Statement: Improve billability from current 60% to 70% while maintaining planned fee adjustment. Problem Statement: Lower than expected billability, also described as Excessive Bench Capacity, results in chargeability variances and negatively impacts services margins by approximately $100,000,000 per year. Lean and Six Sigma Example: Project Report Project Name: Project Leader: Project Champion:
